Responsibility in young years
The 1970s for Brose were a decade of change, new organization and important decisions for the future.
The starting point for this was the second generational change in the company’s history: When Michael Stoschek became leader of the company at the age of 23 years, around 1,000 people were employed. The company generated a turnover of 55 million DM.
In the following three and a half decades, Michael Stoschek develops Brose into an international corporate group that claims market leadership in terms of technology and quality.
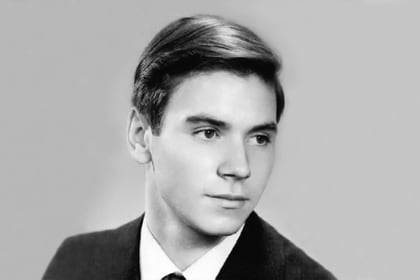
Foray into plastics technology
Brose draws the consequences from the 1973 oil crisis and ventures into uncharted territory: for 15 years, the new plastics technology product area is a strong mainstay. Thermoplastics and polyurethane integral foam (PU) are processed. Products include covers, trim panels, gearshift knobs, as well as armrests and handles, bumper horns and rear spoilers - especially headrests.
Entering the plastics sector is not without risk. Brose is entering a field already occupied by strong competitors with its new product. Brose continues to manufacture thermoplastics to this day. PU production is scaled back in 1984. The last headrest leaves the Coburg plant in 1989. It is number 1,111,111.
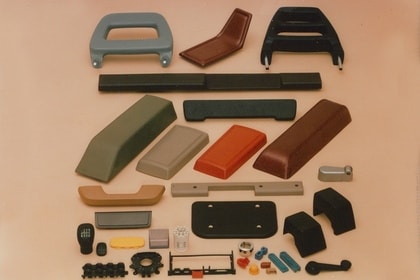
Trendsetter in data processing
October 4, 1973 marks Brose's entry into data processing: on this day, the "IBM 3 Model 15" system goes into operation. At the turn of the year 1988/89, Brose Coburg was the first company in Germany installing the most modern mainframe at the time: the "IBM 3090 18S". When, in 1998, Michael Stoschek decided to use the software SAP for all commercial and logistic processes worldwide and install the respective IT infrastructure, Brose became a trendsetter once more. Brose initiated the most important future-oriented project in the field of information technology under the project name "SPEED". Today, all 65 Brose plants in 24 countries worldwide use this software - and this concept is still exemplary in the industry sector.
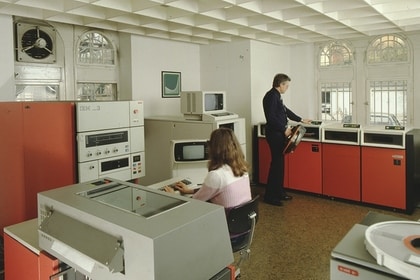
Individual seat adjustments
Brose is the first manufacturer in Europe to develop and produce power seat adjusters.
Beginning in 1979, Mercedes opts for this future-oriented innovation, equipping the S Class with these products. Electromechanics enable the height, length and tilt adjustment of the seat. Later the product scope will be extended to include backrest and headrest adjustments. Other customers include Alfa Romeo, Audi, BMW, Fiat, Ford, Jaguar, Saab and Volvo.
From 1983, Brose equips the seat adjuster with an electronic seat position memory.
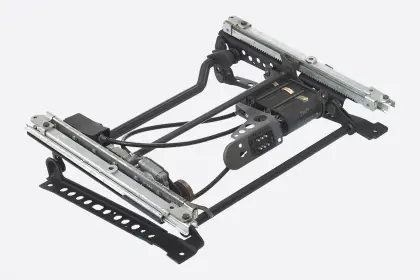
Fasten seat belts!
In 1979 Brose ventures into a new product segment with the development of the electric seat belt transport system (EGT). The EGT automatically wraps the seat belt around driver and front passenger. In the U.S. the tightening of a regulation on passive safety is imminent. This offers Brose the opportunity for a successful market launch. When the bill is overturned, potential customers in Germany are to be won over to the system. But the topic of "seat belt use" divides the nation. After all, the EGT has been used in the U.S. since 1986 in vehicle models from Jaguar and Saab. Although it is not a market success, the EGT fits seamlessly into the line of Brose products which increase comfort and safety in the car.
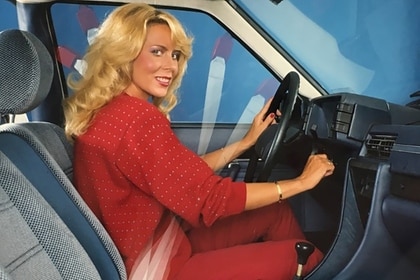
Seat adjusters for King Carl XVI. Gustaf
On October 14, 1982, King Carl XVI Gustaf of Sweden and his wife Silvia paid a visit to the Brose plant during their private stay in Coburg. On this occasion, the guests also "tested" the new generation of multi-way seat adjusters. What could be more natural than to give the monarch car seats with Brose seat adjusters for his BMW? One year later, Michael Stoschek received a letter from the Swedish royal family. In it, Court Director Claes Nordström wrote: "His Majesty the King has instructed me to thank you sincerely for your gift. After using the very practical car seats in the King's BMW for some time, I would like to express his satisfaction with their function".
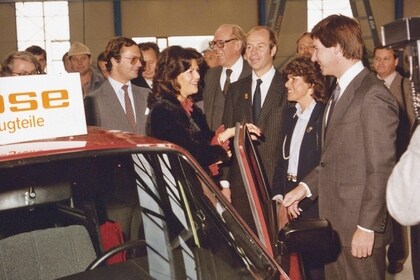
Excellent grades on final certificates
In 1984, Brose is honored by the highest authorities for its exemplary achievements in apprenticeship. Federal President Carl Carstens presents the award to Executive Vice-President Jakob Faßbender on behalf of the Federal Republic of Germany. Word has spread about the high quality of Brose's vocational training: State-of-the-art technical facilities are in use. The apprentices prepare intensively for their exams in in-house classes. Even sports are on the schedule. Interesting excursions are undertaken. Customer plants are visited or seminar weeks are organized. The training is well-founded and fun. That's why the grades are above average: often, the final certificates show excellent grades. To this day, Brose apprentices are among the best in their Chamber of Industry and Commerce examinations.
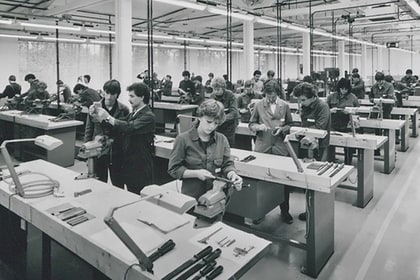
Once solitary workers, today team players
In March 1985, the first robot started its work in the die-casting foundry in Coburg. "Mantec r3" helps with the production of die-cast aluminum plates for window regulators. The fast and inexpensive production speaks for the robot and it improves workplace ergonomics and efficiency.
The "Mantec r3" did not remain solitary for long: In 1987, the training workshop received its first training robot. From that time onwards, the apprentices were able to concern themselves intensively with this new technology. Nowadays collaborating robots have an important role in our assembly: They do exhausting tasks such as lifting heavy seat structures and allow for the automation of routine tasks.
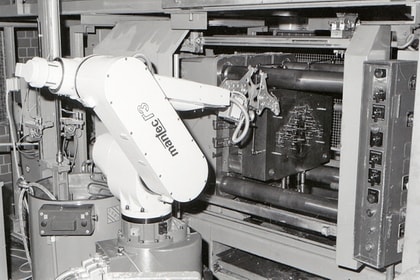
World novelty for more comfort and safety
Brose’s development of the world’s first electronic control-unit for power window regulators in 1986 paved the way for moving into the field of mechatronics: apart from its express up and central closing/opening comfort functions, the electronic “anti-trap feature” has sensors to detect obstacles, allowing the closing window to stop and reverse.
Today, this technology has become a worldwide standard.
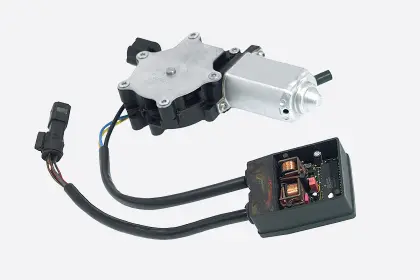
The key to success
With its modular vehicle door, Brose ventures into new territory in terms of technology and logistics: the concept is first used in the Audi 80 Coupé in 1987.
Brose proceeds not only to develop and produce the most important door components, but also to integrate them into a complete system using sophisticated logistics to ensure that the pre-tested products are ready on schedule for installation at the car manufacturer’s assembly line.
Once again, Brose plays a pioneering role in the market.
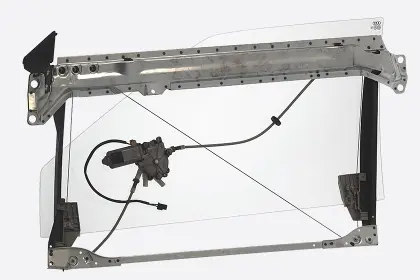
Internationalization
The markets are growing together; supply and demand know no geographic boundaries.
Anyone who wants to be successful in the automotive business has to operate internationally. At the end of the eighties, Brose establishes its first two foreign production sites in England and Spain. In 1993, the first manufacturing facility on the American continent comes into operation in Querétaro/Mexico.
In the following years, sales and engineering offices are set up in Detroit, Tokyo and Paris.
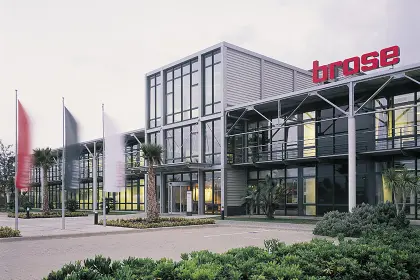
The role model
When Brose's manufacturing capacities in Germany reach their limits, the shareholders decide to set up another production site.
Established in 1997, the plant in Meerane/Saxony is the first location for producing and supplying door systems sequenced to the car manufacturer’s production schedule and delivered directly to its assembly line.
This location is to become a pioneer in the years ahead for all subsequent JIS plants of the Brose Group in Germany and abroad.
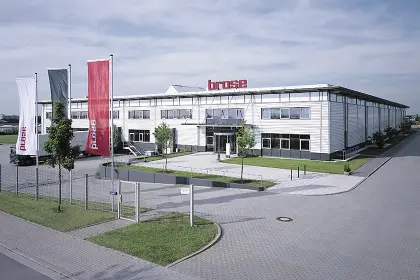
Door systems in minute intervals
At 10:29 p.m. on Sunday, April 13, 1997, the first sequence call-off from the VW plant in Mosel heralds a new era at Brose: Just-in-sequence production and delivery of door systems. Short-term, on-demand production avoids expensive warehousing and long transport routes and is an important competitive factor. While the assembly of the vehicle has already begun at VW, the assembly of the associated door systems is starting at Brose. The maximum time between call-off and installation in the vehicle is 210 minutes. A sophisticated logistics concept identifies three alternative routes and ensures punctual delivery.
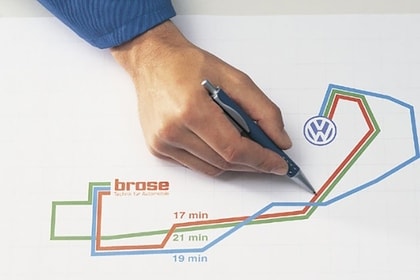
Brose redefines working world
At the Coburg headquarters, this is documented in the largest modernization program in the company's history: the "face" of Brose real estate is changing fundamentally. Even behind the facades, nothing remains as it was: with the "New Working World" concept, Brose is redefining workplace design as well as administrative processes and creating structures that are considered exemplary in the industry. Key elements are state-of-the-art office technology, variable working hours, a performance-based pay system and attractive social benefits. Combined with the uniform global corporate design, this leads to an increased identification of employees with the company and strengthens their motivation and shared responsibility.
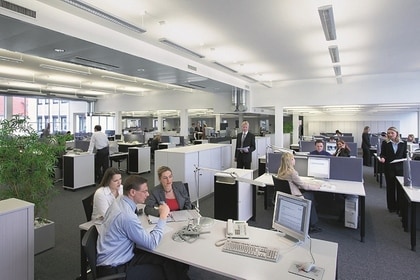
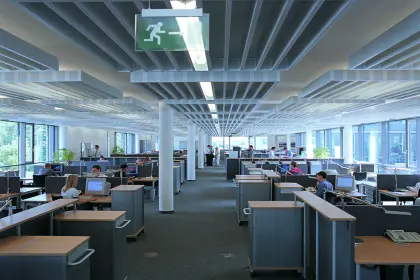
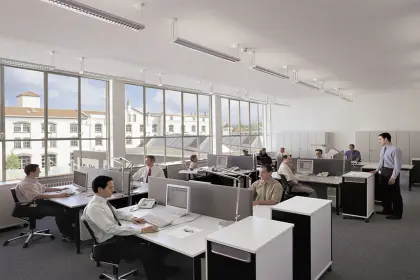
Systematic closure technology
Through the acquisition of the closure system business from Bosch in 2002, Brose again extends its competence in the vehicle door.
Brose latch modules combine the door latch, inside handle and all mechanical and power connections into one sub-assembly, resulting in less effort when opening and less noise when closing the door as well as improved anti-theft protection. Delivery as a pre-tested unit shortens installation time at the car manufacturer’s assembly line.
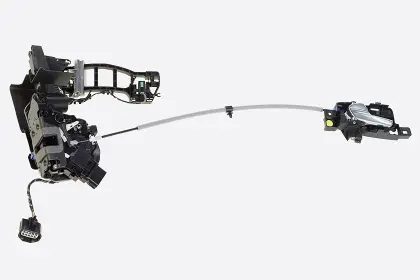
Competitive in the global market
In the age of globalization, the competitive edge that the company has acquired thanks to its innovative spirit, quality and efficient project management must be extended, especially in high-wage Germany, through even greater cost efficiency: whether through the further development of products, global procurement, personnel costs or the continuous optimization of production processes. For example, the degree of automation depends on the specific personnel costs of the worldwide locations.

Uniform corporate design
In the course of its expansion, Brose has built plants all over the world according to a uniform corporate design. Employees on four continents work in nearly identical environments and adhere to the same organizational models and production principles.
The functional design of the production and administrative buildings focuses on optimized processes, short distances and a clearly structured layout to ensure the highest levels of efficiency, flexibility and systematic operation. Uniform corporate image and systematic work processes promote the definition of Brose’s brand in the automotive-supplier industry and help its employees identify with the family-owned company.
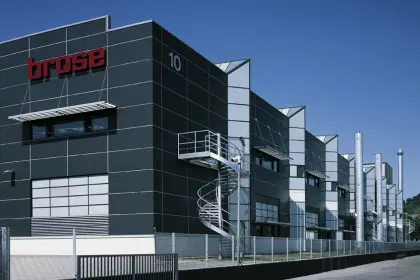
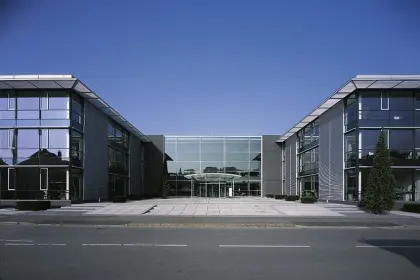
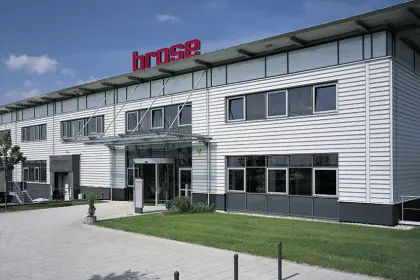
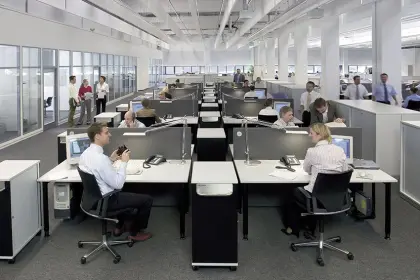
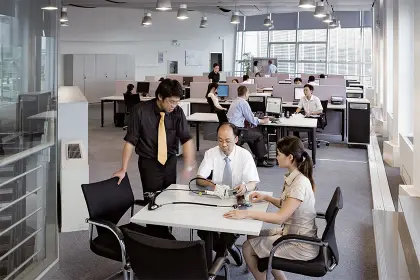
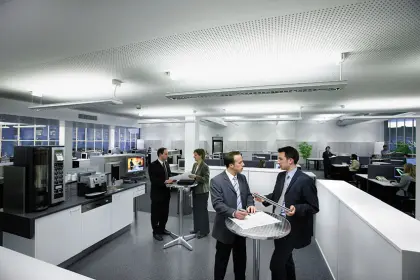
Change in leadership
When Michael Stoschek hands over the CEO post - after more than 34 years at the helm - to Jürgen Otto in 2005, the company closes on its most successful year ever: Brose generates a turnover of 2.2 billion euros and approx. 8,900 employees work at 37 locations in 19 countries.
The appointment of Jürgen Otto, who has 15 years of experience in various managerial functions at the company, means that, for the first time ever, there is a non-family member running the company; nevertheless it still underscores the continuity and long-term perspective of the Brose Group.
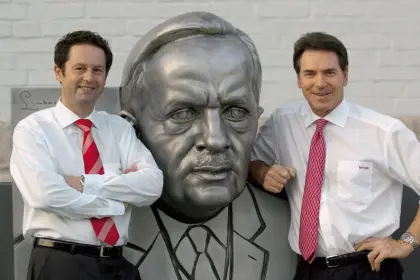