Building Excellence Together
Help shape the future of mobility – with innovative technologies and pioneering solutions that change the market. We offer tailor-made entry opportunities and individual career prospects.
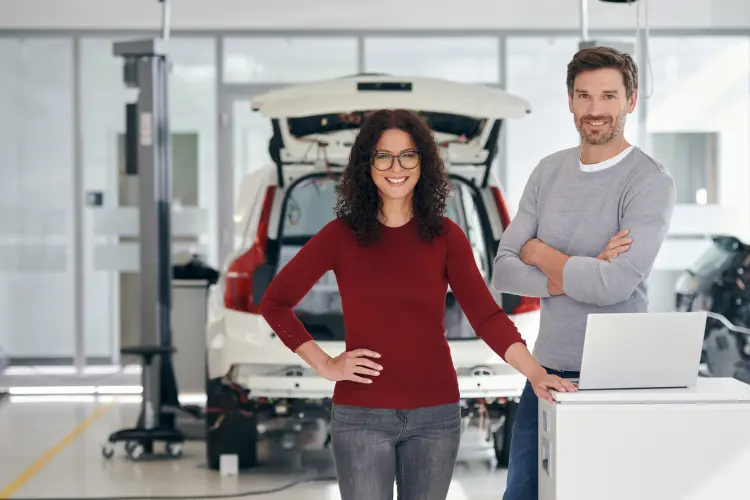
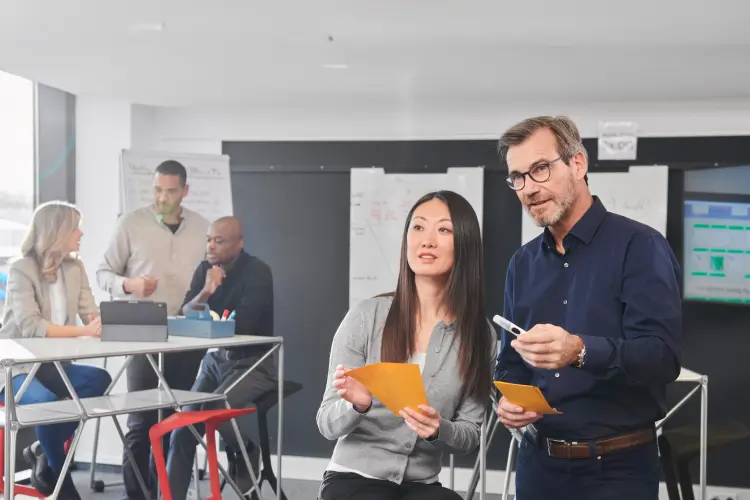

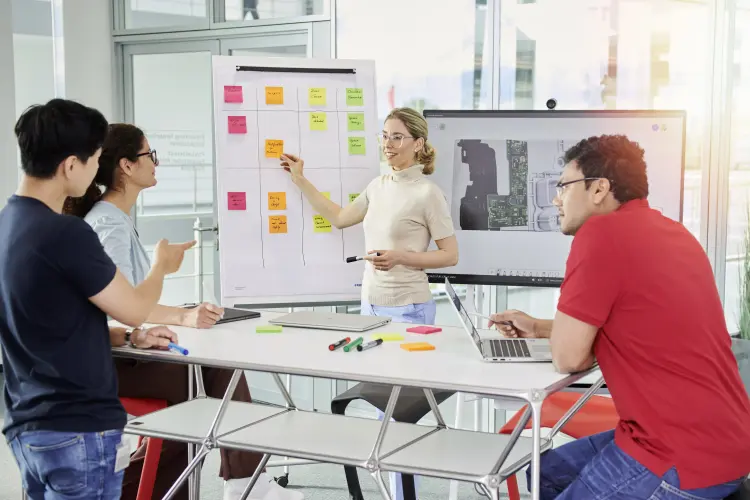
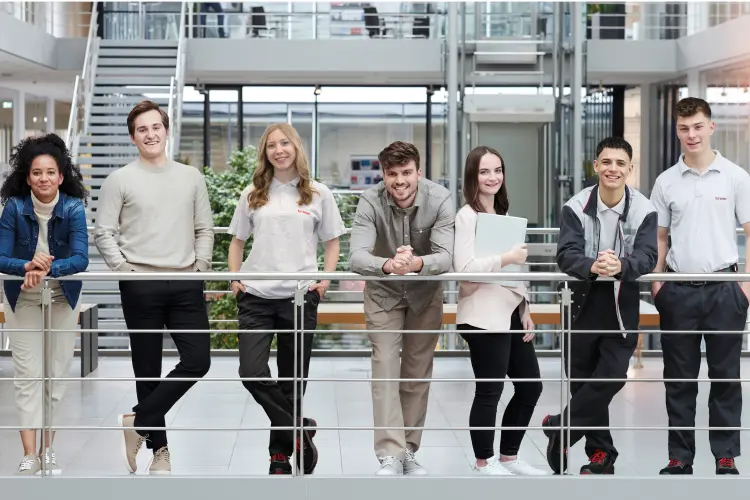
Help shape the future of mobility – with innovative technologies and pioneering solutions that change the market. We offer tailor-made entry opportunities and individual career prospects.
Your chosen job offer is only available in another language.
Open job offer