Brose is one of the five largest family-owned automotive suppliers.
- Employees
- 31,000
- Locations
- 68
- Countries
- 24
Mechatronic components and systems
The core competence of Brose is the synthesis of mechanical, electrical and electronic systems. Worldwide, every third new vehicle is equipped with at least one Brose product.
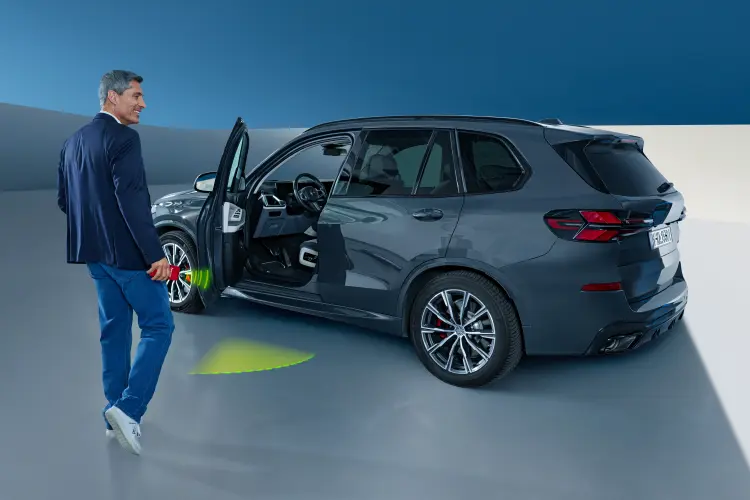
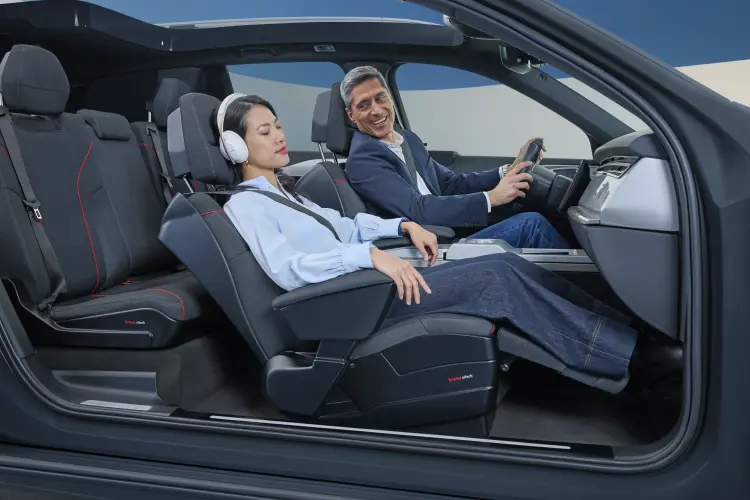
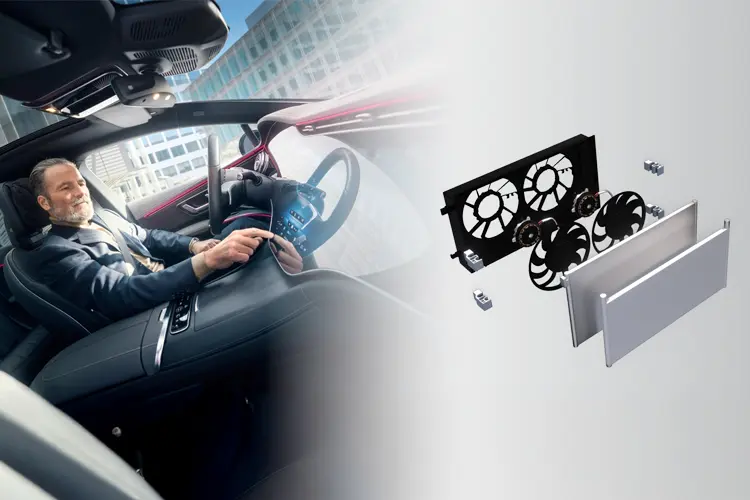