Brose gehört zu den fünf größten Automobilzulieferern in Familienbesitz.
- Mitarbeitende
- 31.000
- Standorte
- 68
- Länder
- 24
Mechatronische Komponenten und Systeme für Automobile
Die Kernkompetenz von Brose liegt in der Verbindung von Mechanik, Elektrik und Elektronik. Jeder dritte Neuwagen weltweit ist mit mindestens einem unserer Produkte ausgestattet.
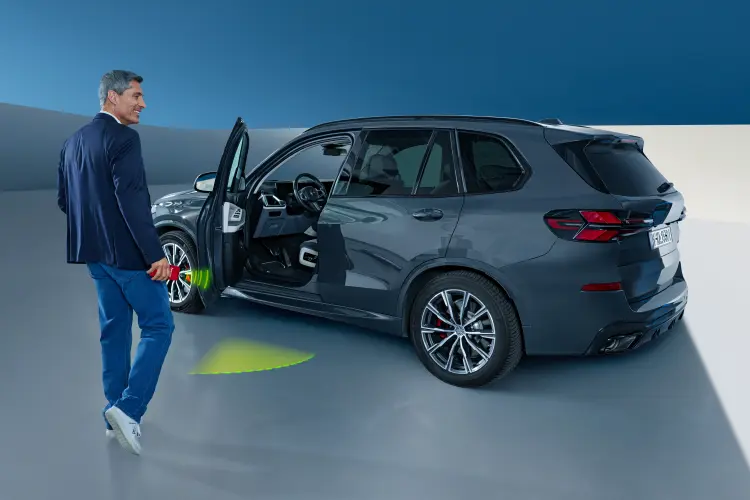
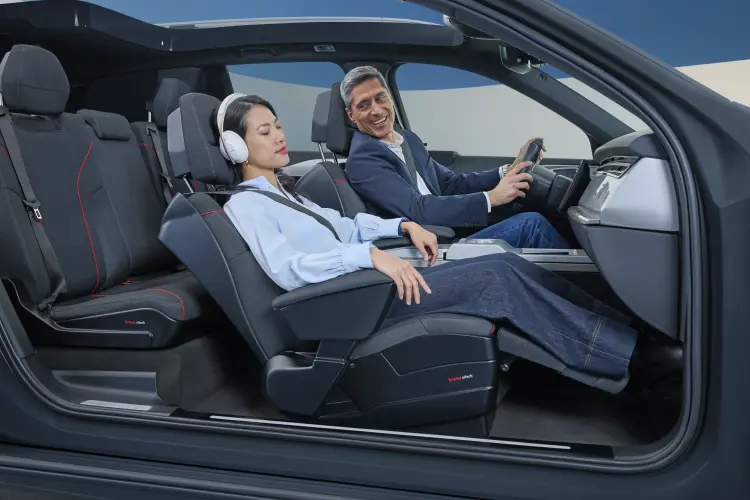
_rebrush750500.webp)